عنا
مرحبا هل يمكنني مساعدتك؟
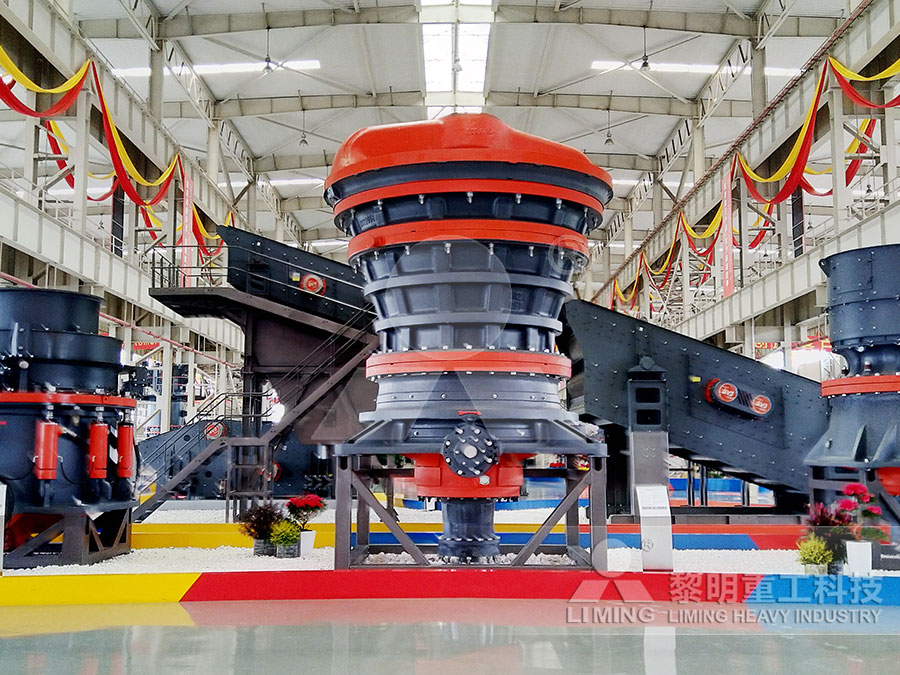
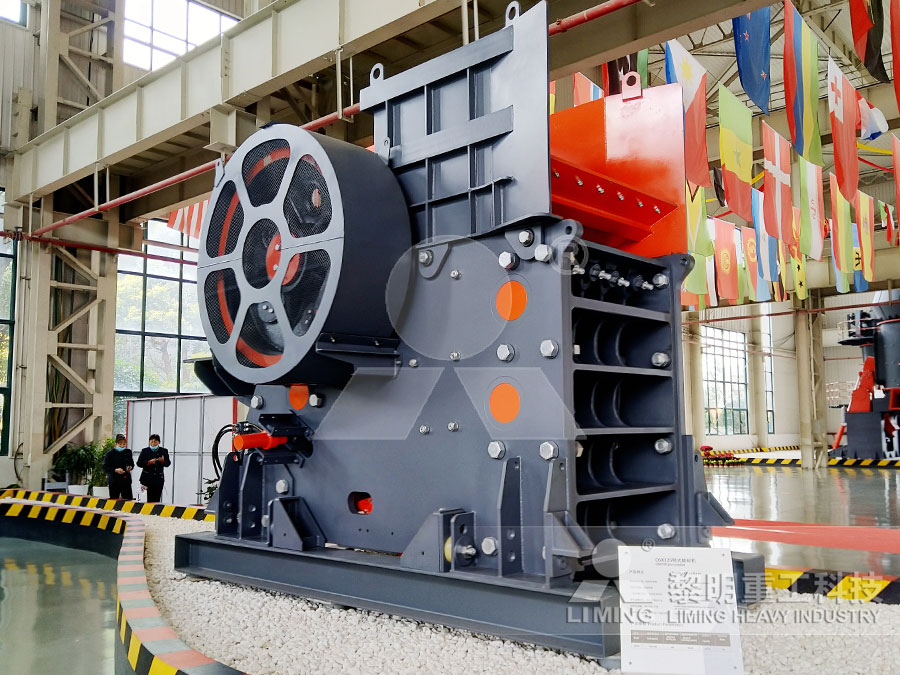
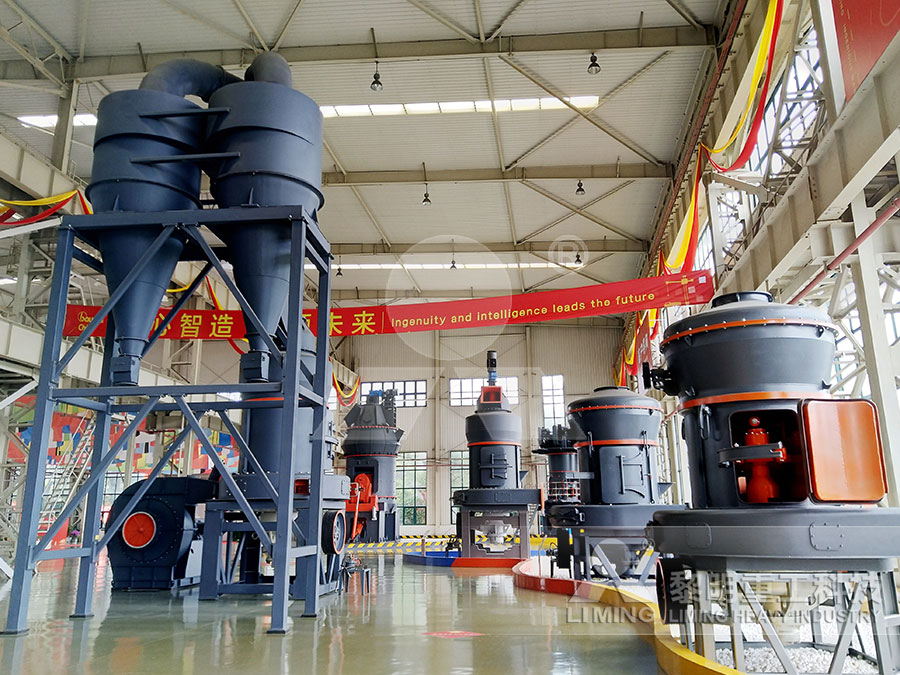
تأسست شركة Liming Heavy Industry في عام 1987 ، وتقع في منطقة Pudong الجديدة ، شنغهاي ، الصين ، وتغطي أكثر من 200000 متر مربع بما في ذلك العديد من الشركات التابعة. يتعلق العمل الرئيسي بالعديد من المجالات ، مثل تكسير المناجم ، وسحق المباني ، والطحن ، وصنع الرمل ، والتكسير المتنقل ، وما إلى ذلك. الكسارة ، الكسارة المخروطية الهيدروليكية عالية الكفاءة من سلسلة HPT ، المطحنة الأوروبية شبه المنحرفة MTW ، المطحنة العمودية LM ، المطحنة الأسطوانية العمودية فائقة الدقة من سلسلة LUM ، الكسارة الصدمية ذات المحور الرأسي VSI5X ، ومعدات نظام VU.
يجلب Liming عددًا كبيرًا من المواهب الذكية والإبداعية معًا الذين يقدمون منتجات مبتكرة باستمرار. أخذت الشركة زمام المبادرة في الحصول على شهادة نظام الجودة الدولية ISO9001: 200 ، وشهادة الاتحاد الأوروبي CE وشهادة GOST الروسية ، وقد حصلت على 106 براءة اختراع وطنية بما في ذلك 4 براءات اختراع ، و 12 براءة اختراع تصميم و 90 براءة اختراع لنماذج المنفعة حتى الآن. إلى جانب ذلك ، هناك العديد من الجوائز مثل جوائز العلوم والتكنولوجيا في صناعة الآلات الصينية ، وجوائز الإنجاز العلمي والتكنولوجي في المقاطعات ، والمنتجات الصناعية الموفرة للطاقة في قائمة شرف ليمينغ.
من أول جهاز خروج تم تركيبه وتصحيحه بنجاح في كازاخستان إلى أول خط ذكي لتصنيع الرمل يعمل بسلاسة في المملكة العربية السعودية ، قدمت Liming خدماتها لـ 140 دولة ومنطقة ، مثل روسيا وكازاخستان وأذربيجان وتركيا والكويت وجنوب إفريقيا ومصر ، لا يمكن تجاهل فيتنام وماليزيا والهند وأستراليا وكوريا وكندا والاتحاد الأوروبي ، وما إلى ذلك ، وقوة الشركة في آلات التعدين العالمية بعد الآن.
رسالة عبر الإنترنت
مرحبا هل يمكنني مساعدتك؟
manufacturing of powder by dry ball mill process
2022-05-03T12:05:54+00:00
Manufacturing Of Cement By Dry And Wet Process
Burning: In this operation, the slurry is directly fed into a long inclined steel cylinder called a Rotary kilnIn this kiln there are 3 different zones shown in fig below Cement Manufacturing Process Flow Chart (i) Drying Zones: In the wet process, the drying zone is comparatively larger than the dry process It is because the raw material in slurry form is directly fed into the kiln which Fig 51 shows the typical grain size and the secondphase precipitates of alloys manufactured by the powder process advanced powder metallurgy tubing (APMT) and by traditional melting, casting, and forging (C26M) As for other family of alloys, the microstructure of FeCrAl alloys would vary considerably depending on their manufacturing path Powder Process an overview ScienceDirect Topics In the production of ethanol, wet ball milling is the process used, because of its versatile process It produces more products than dry ball milling, but in terms of efficiency, capital, and operating cost, most ethanol plants in the USA prefer to use dry ball milling process In other words, dry ball Wet Ball Milling Vs Dry Ball Milling Orbis Machinery,

Understanding The Dry Granulation Process
The original method of dry granulation employed a heavy duty tablet press to compact the dry powder The compacting process in this case is known as slugging and the compacted material was therefore in the form of “slugs” typically 25 mm in diameter and 1015 mm thick A hammer mill Ball milling technique, using mechanical alloying and mechanical milling approaches were proposed to the word wide in the 8th decade of the last century for preparing a wide spectrum of powder materials and their alloys In fact, ball milling process is not new and dates back to more than 150 years It has been used in size comminutions of ore, mineral dressing, preparing talc powders and many Ball Milling an overview ScienceDirect Topics Manufacturing of aluminum flake powder from foil scrap by dry ball milling process SeongHyeon Hong*, DongWon Lee, ByoungKee Kim Department of Materials Engineering, Korea Institute of Machinery and Materials, 66 Sangnam, Changwon, Kyungnam, 641010, South Korea Received 20 August 1998 AbstractManufacturing of Aluminum Flake Powder From Foil

Manufacturing of aluminum flake powder from foil
Manufacturing of aluminum flake powder from foil scrap by dry ball milling process Author links open overlay panel SeongHyeon Hong DongWon Lee ByoungKee Kim Show more The aluminum flake powder produced by the dry ball milling of aluminum foil scrap can be applied to fingerprint detection or to aerate lightweight concrete In dry milling, about 25 vol% of powder is added along with about 1 wt% of a lubricant such as stearic or oleic acid For wet milling, 3040 vol% of powder with 1 wt% of dispersing agent such as water, alcohol or hexane is employed • Optimum diameter of the mill for grinding powders is about 250 mm Ball MillPowder metallurgy – basics applications The milling time, the ball size (diameter 96 or 16 mm), the number of intermediate stops during milling for 25 h, and the content of stearic acid were varied in the dry ball milling process Aluminum flake powder of 1 g during the milling was sampled and characterized The mean size, the size distribution and the specific surface area of Manufacturing of aluminum flake powder from foil

Ball Milling Material Milling, Jet Milling AVEKA
Ball milling is a size reduction technique that uses media in a rotating cylindrical chamber to mill materials to a fine powder As the chamber rotates, the media is lifted up on the rising side and then cascades down from near the top of the chamber The ball mill process parameters discussed in this study are ball to powder weight ratio, ball mill working capacity and ball mill speed As Taguchi array, also known as orthogonal array design, adds a new dimension to conventional experimental design, therefore, Orthogonal array (L9) was carefully chosen for experimental design to understand Comparative Study on Improving the Ball Mill Process Spray Dried Powder Spray drying is a method of producing a free flowing, uniform, granulated powder, which is the ideal feedstock for a variety of pressing processes, such as uniaxial pressing and wet and dry–bag isostatic pressing The raw material blend is firstly milled in a ball mill in a solvent, such as water, using ceramic ballsAdvanced Ceramics Manufacturing Processes

Surface coating copper powder with carbon
The mechanical dry coating technique was used to fabricate CNT coatings (guest particles) on the surface of copper (Cu, host) particles using a traditional ball mill and a stirred ball mill The coatings were produced under various experimental conditions (varying rotation speed and grinding duration, with a ball diameter of 5 mm), and the Process: 2 Dry Granulation with Roll Compactor System Powder Row Material Grading sieving Process (Machine – Vibro Sifter) Dry Compaction of the material (Machine – Roll Compactor) Compacted material to be granulated (M/c Oscillating Granulator/Multi Mill) Grading sieving (Machine – Vibro Sifter) Lubrication of granules for free flowing (M/c Blender Octagonal / Double V Pharmaceutical Manufacturing Process : Pharma Focusing on the research and development and innovation of mineral processing equipment, Xinhai has won more than 100 national patents, strives for perfection, strives to complete the combination of equipment and technology, improve productivity, reduce energy consumption, extend equipment stable operation time, and provide costeffective servicesMineral Processing, Equipment Manufacturers, Ball
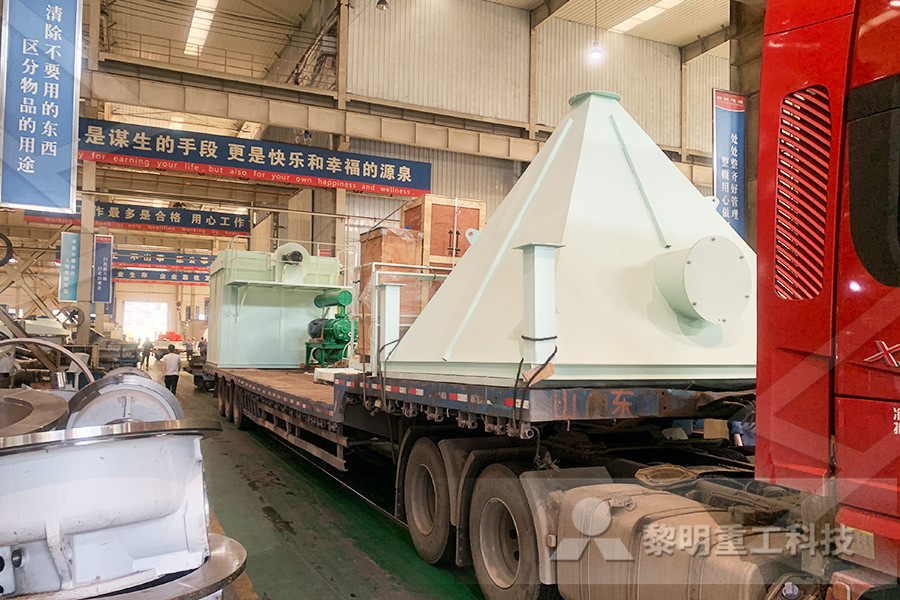
Process optimization and particle engineering of
Process control and optimization is a critical aspect of process analytical technology (PAT), quality by design (QbD), and the implementation of continuous manufacturing procedures While process control and optimization techniques have been utilized in other manufacturing industries for decades, the pharmaceutical industry has only recently begun to adopt these proceduresAdvantages of Dry process Spray dryer could be eliminated; Power supplied and water supplied to spray drier could be avoided Initial capital is less compared to wet process; DisAdvantages of Ball mill The product will be of low strength when compared to wet process The finishing will not be as good as product obtained in wet process Tiles Tile Manufacturing/Production Process By Later, the dry process gained momentum with modern development of technique’s 5 Wet process • Wet process : In this process, the raw materials are changed to powdered form in the presence of water In this process, raw materials are pulverized by using a Ball mill, which is a rotary steel cylinder with hardened steel ballsManufacturing of portland cement SlideShare

Manufacturing process of cement Wet Process
Jul 9, 2020 cement manufacturing process, cement production process, clinker, flow diagram of cement production, manufacturing process of cement by wet process, preheating tower Cement is the most significant material used in construction and it acts as a binder that can adhere to the materialsBall milling is a size reduction technique that uses media in a rotating cylindrical chamber to mill materials to a fine powder As the chamber rotates, the media is lifted up on the rising side and then cascades down from near the top of the chamberBall Milling Material Milling, Jet Milling AVEKA In dry and semi dry processes for manufacturing of cement, the raw materials are crushed and fed in the correct proportions into a grinding mill The raw materials are dried and reduced in size to a fine powder in to grinding mill The dry powder is called the raw meal The raw meal is Dry Process for Manufacturing of Cement GharPedia
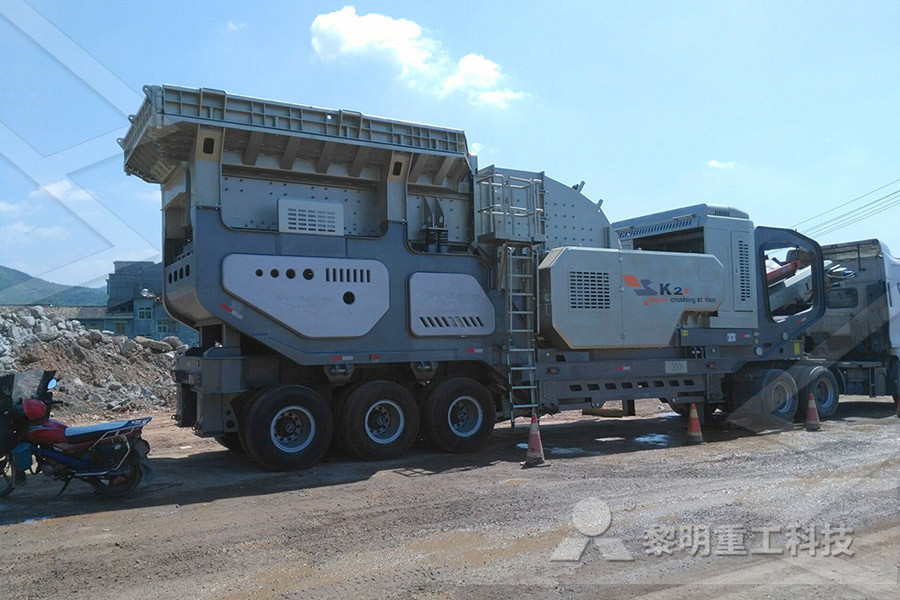
Comparative Study on Improving the Ball Mill Process
The ball mill process parameters discussed in this study are ball to powder weight ratio, ball mill working capacity and ball mill speed As Taguchi array, also known as orthogonal array design, adds a new dimension to conventional experimental design, therefore, Orthogonal array (L9) was carefully chosen for experimental design to understand Spray Dried Powder Spray drying is a method of producing a free flowing, uniform, granulated powder, which is the ideal feedstock for a variety of pressing processes, such as uniaxial pressing and wet and dry–bag isostatic pressing The raw material blend is firstly milled in a ball mill in a solvent, such as water, using ceramic ballsAdvanced Ceramics Manufacturing Processesthe handmade powder and the early mill powder were what is termed as 'serpentine,' or powder that was only incorporated and dried The incorporating step of the process was the first and most important From hand mortar and pestle of the laboratory we proceed to spring poleactuated (refer to Fig 10) stamping This process becameBlack Powder Manufacture

Pharmaceutical Manufacturing Process : Pharma
Process: 2 Dry Granulation with Roll Compactor System Powder Row Material Grading sieving Process (Machine – Vibro Sifter) Dry Compaction of the material (Machine – Roll Compactor) Compacted material to be granulated (M/c Oscillating Granulator/Multi Mill) Grading sieving (Machine – Vibro Sifter) Lubrication of granules for free flowing (M/c Blender Octagonal / Double V Focusing on the research and development and innovation of mineral processing equipment, Xinhai has won more than 100 national patents, strives for perfection, strives to complete the combination of equipment and technology, improve productivity, reduce energy consumption, extend equipment stable operation time, and provide costeffective servicesMineral Processing, Equipment Manufacturers, Ball Advantages of Dry process Spray dryer could be eliminated; Power supplied and water supplied to spray drier could be avoided Initial capital is less compared to wet process; DisAdvantages of Ball mill The product will be of low strength when compared to wet process The finishing will not be as good as product obtained in wet process Tiles Tile Manufacturing/Production Process By

Manufacturing process of cement Wet Process
Jul 9, 2020 cement manufacturing process, cement production process, clinker, flow diagram of cement production, manufacturing process of cement by wet process, preheating tower Cement is the most significant material used in construction and it acts as a binder that can adhere to the materials Process control and optimization is a critical aspect of process analytical technology (PAT), quality by design (QbD), and the implementation of continuous manufacturing procedures While process control and optimization techniques have been utilized in other manufacturing industries for decades, the pharmaceutical industry has only recently begun to adopt these proceduresProcess optimization and particle engineering of